Technological and Developmental Capabilities
The insatiable challenge to propose "plus-alpha" solutions
At IL Engineering Management, we work with our customers to create completely tailor-made machinery and equipment from scratch to meet their needs. We will not only accomplish what you request, but also respond to your needs with our engineers' challenge to provide you with a plus α proposal.
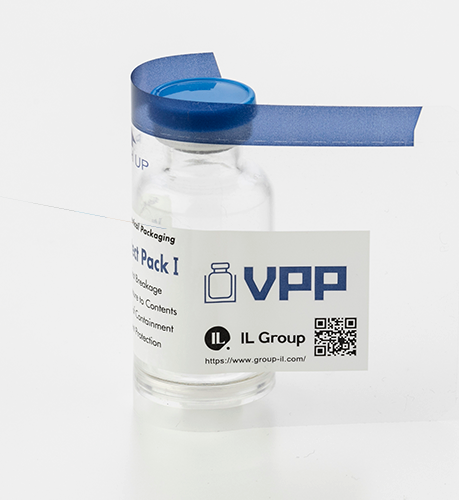
Allowable width Evolution up to approx. 22 mm in diameter
"Vial Protect Pack (VPP)" is the culmination of the technologies of IL Pharma Packaging, a tack label manufacturer and distributor, and IL Engineering Management, a label applicator.
This product is used to attach labels printed with lot numbers and other information to injection drug containers. After wrapping a plastic cup containing a vial bottle with a label whose properties shrink with heat, the label is heat-shrunk to cover the entire container.
The VPP is widely used in the medical and other industries because it has not only the original function of attaching a label to a vial, but also has additional functions such as preventing damage to the vial and protecting the internal liquid by cutting UV rays. At the time of the development of VPP, we already had over 20 years of experience in manufacturing labeling machines since the 1990s, and we had the technological capability to meet the needs of the times.
We began joint development based on this technology, but there was a conflict between the shrinkage rate of labels due to heating and the diameter of the product to which the label was to be applied. The allowable width of product diameter that could be labeled with a single unit of equipment used to be about 15 mm, but now it is possible to label products as large as 22 mm or more.
This is the result of our relentless challenge to create something that no one has yet created.
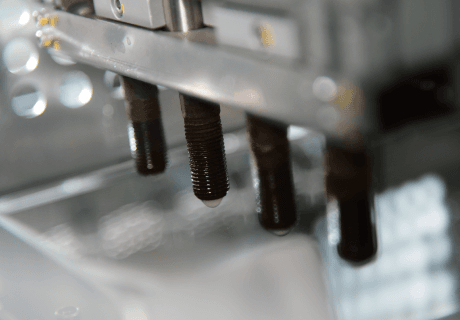
20% increase in production efficiency
Request for improvement of a hardening machine for hub bolts used to fasten automobile tires. The customer's request was for "cost reduction through factory automation."
The request was to automate the power required to feed 3,750 hub bolts per box into the hardening machine, thereby reducing labor costs. The conventional six-second process of feeding two hub bolts into the machine was reduced to five seconds. After that, it took another 5 seconds to feed in 4 bolts.
The success of IL Engineering Management's challenge to provide "plus alpha proposals," such as improving production efficiency, leads to higher expectations and demands from our customers.
In our company, this ignites the spirit of our engineers and becomes the driving force to challenge new possibilities.
The repetition of this cycle leads to the evolution of technology, and is the force that leads us to the best answer for our customers.
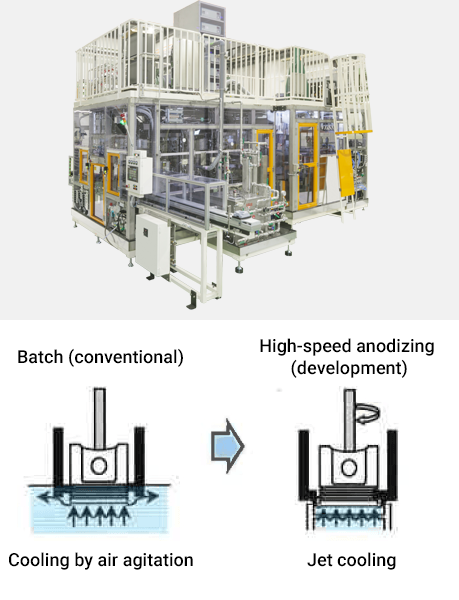
Reduces processing time by a factor of 24
Pistons used in automobile engines are manufactured through a number of processes, including metal forming and surface treatment.
If this process can be made in-line (integrated production), the time lag can be reduced and parts can be manufactured more efficiently.
Our company was contracted to provide anodizing equipment for the tops of pistons.
Previously, multiple pistons were processed in batches, but in order to achieve in-line production, it was necessary to process each piston in a short time.
In order to anodize the parts in a short time, it was necessary to increase the electric current applied to the parts, but the heat generated by the high current would reduce the quality of the product. To solve this problem, we devised a method in which the piston to be processed is rotated at high speed and the processing fluid is injected onto the surface. The cooling effect of high-speed rotation is dozens of times greater than that of conventional methods, minimizing heat generation even when 24 times more current is applied than with conventional methods.
The ability to apply 24 times the current means that the time required for processing is reduced by a factor of 24.
In addition, we have reduced the size of the facility to one-twelfth the floor space required for the facility. This was a success that far exceeded the customer's target of one-third.